The causes and solutions of bronze casting segregation can be summarized as follows:
Causes of segregation
1. Alloy solidification characteristics: During the solidification process of the alloy, due to the different crystallization temperatures of each element, microsegregation and positive segregation will occur.
2. Cooling rate: Cooling rate has a significant impact on segregation, and a faster cooling rate may cause segregation to intensify.
3. Alloy composition: The difference in specific gravity of different components in the alloy and the mutual solubility of the liquid alloy can also cause segregation. For example, when bronze-aluminum alloys are immiscible in the liquid state, delamination will occur.
4. Process control: Improper control of process parameters such as temperature control, cooling rate, and tensile force during continuous casting and rolling can also cause segregation.
5. Uneven stirring: Uneven stirring will cause the alloy to form an uneven crystal structure during the solidification process, thereby causing segregation.
Solution
1. Optimize alloy design: When designing alloys, consider the balance and compatibility of each element, select an appropriate alloy formula, and avoid element combinations with a greater tendency of segregation.
2. Refine grains: Refine grains and increase crystal nucleation, which can effectively reduce forward and reverse segregation.
3. Homogenization treatment: The casting is heat-insulated at a certain temperature to move the solute elements of different concentrations within the crystal, and finally achieve uniform composition within the crystal.
4. Control the cooling rate: Appropriate control of the cooling rate, such as increasing the cooling intensity, lowering the pouring temperature, strengthening secondary cooling, etc., can increase the cooling rate and reduce segregation.
5. Optimize process parameters: Optimize process parameters of continuous casting and rolling, such as temperature control, cooling rate, tensile force, etc., to reduce the occurrence of segregation.
6. Use directional solidification technology: This technology can effectively control the crystal growth direction and reduce the occurrence of segregation.
7. Online monitoring and control system: Establish an online monitoring system for segregated elements to monitor the uniformity of alloy components in real time and adjust process parameters in a timely manner to control the occurrence of segregation.
8. Use appropriate refining agents and grain regulators: For example, adding grain regulators such as rare earth elements can improve the grain refinement of bronze and reduce the occurrence of segregation.
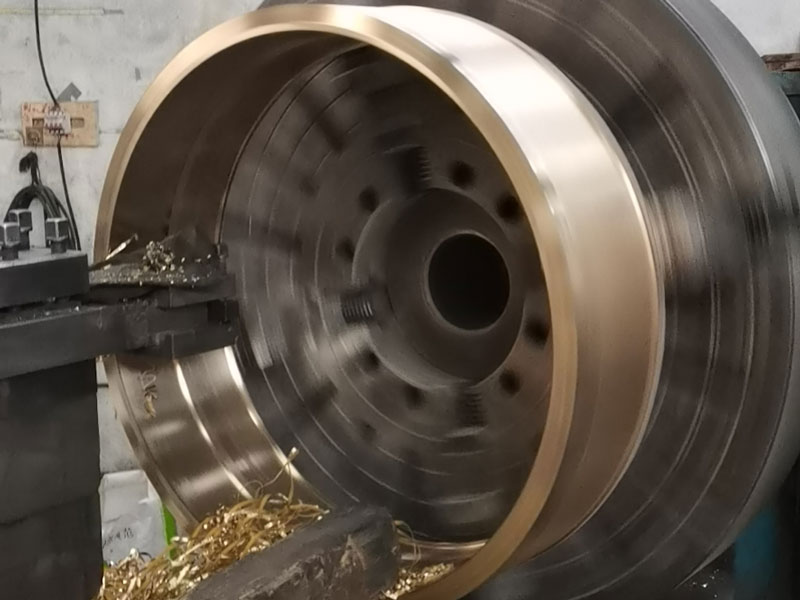
Please note that solving the segregation problem of bronze castings requires comprehensive consideration of multiple factors and taking corresponding process measures based on the actual situation. In actual operation, it is recommended to consult professional casting engineers or technicians to ensure the effectiveness and feasibility of the solution.