There are many processes for
copper casting, the most common ones include the following:
1. Sand casting method: using various types of sand as mold materials, with low cost and easy operation. It is suitable for castings of various sizes and shapes, especially for making medium and small castings.
2. Metal mold casting method: a method of casting copper by making metal materials into molds. The advantages of this method are long mold life, high dimensional accuracy of castings, good surface quality, and suitable for mass production.
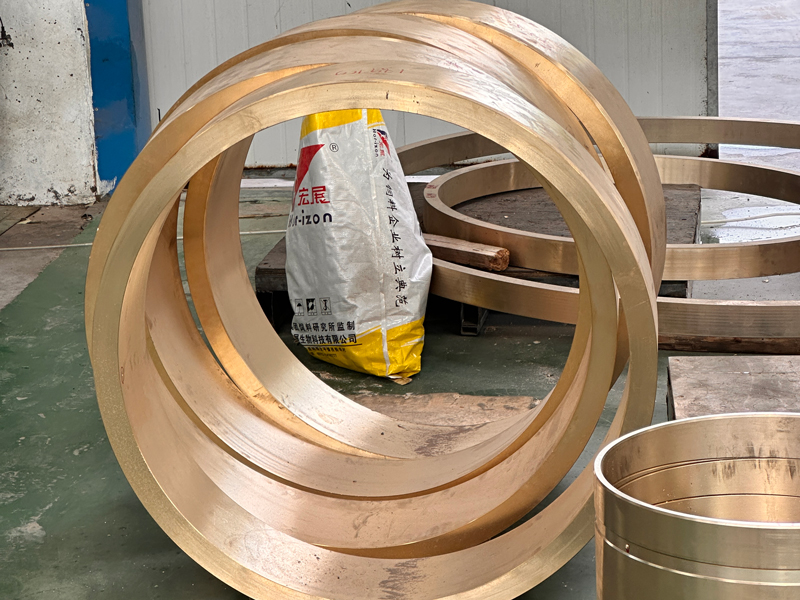
3. Pressure casting method: an efficient and large-scale copper casting process, which injects molten copper into the mold under high pressure, quickly cools and solidifies, and has high production efficiency and low cost.
4. Centrifugal casting method: using centrifugal force to pour molten copper into a rotating mold, so that the copper liquid is evenly distributed and cooled and formed under the action of centrifugal force. This method can produce castings with high mechanical properties and surface quality.

5. Vacuum suction casting method: sucking molten copper into the mold under vacuum, so that the copper liquid is evenly distributed and cooled and formed in the vacuum. This method can produce castings with low porosity and high density.
6. Ceramic mold casting: One of the oldest casting techniques in my country, using clay to make molds, after mold making, roasting and other steps, and finally casting.
7. Filament casting: A special casting process, often used to produce filamentary copper castings, such as the conductor core of wires and cables. This process involves pulling a filament from the surface of molten copper, then lifting the filament from the liquid surface, and breaking it after the copper wire cools and solidifies to obtain the required copper casting.
8. Lost wax method: An ancient copper casting process, using wax as a mold material, heating and melting the wax, then pouring in copper liquid, and demolding the casting after the copper cools. The lost wax method can produce very fine castings, especially suitable for making complex and fine patterns and decorations.

The specific choice of which process needs to be considered comprehensively based on a variety of factors such as the shape, requirements, production scale and production cost of the copper casting.