Details and quality in
bronze casting: the key to success or failure of a work
bronze casting is a long-standing craft. From ancient civilizations to modern art, bronze has always occupied an important position in human culture. Today, bronze casting technology is not only used for the creation of artworks, but also widely used in industry, construction and the manufacture of daily necessities. However, in the bronze casting process, details and quality are the key factors that determine the success or failure of the work. This article will explore the important details in the bronze casting process and how to ensure the high quality of the finished product.
1. Selection of raw materials
The first step in bronze casting is to choose the right raw materials. The purity and alloy composition of bronze directly affect the quality and performance of the casting. bronze alloys (such as bronze and brass) are often used in casting because they have higher strength, corrosion resistance and better plasticity. Inferior materials or alloys with inappropriate composition can cause the finished product to be brittle, easy to crack or rough on the surface. Therefore, when selecting bronze alloys, it is necessary to ensure that the purity and composition of the material meet the expected standards.
2. Mold design and production
The mold is a vital part of the casting process. Whether it is traditional sand casting or modern precision casting, the design and production of the mold directly affect the appearance and fineness of the finished product. When designing the mold, the size, shape, texture and other details of the product should be considered to ensure that the bronze liquid can flow evenly into the mold cavity during the casting process to form the expected shape. In addition, the durability and precision of the mold also determine the mass production capacity and quality consistency of the product.
3. Melting and pouring process
bronze has a high melting point of about 1083℃, and the melting process requires precise control of temperature and time to ensure the uniformity of the bronze liquid. Too high or too low temperature will affect the fluidity of the bronze liquid and the structure of the final product. During the pouring process, it is also important to maintain the preheating temperature of the mold to prevent the bronze liquid from cooling too quickly during the flow process, resulting in incomplete castings or defects such as bubbles and cracks.
4. Cooling and demolding
During the cooling process of the casting, the metal will shrink inside. In order to avoid deformation or cracking of the casting, the cooling rate and method must be carefully controlled. Usually, the casting needs to be cooled gradually, especially large and complex bronze products, which take longer to cool. When demolding, the operation should be cautious to avoid damaging the surface of the casting or causing the details to fall off.
5. Post-processing and finishing
Even if the bronze casting process is perfect, the casting still needs post-processing. Steps such as grinding, polishing, and pickling are used to remove defects and oxide layers on the surface of the casting to improve the smoothness and beauty of the finished product. In addition, some high-end bronze castings will also undergo surface treatments such as gold plating, coloring or anti-corrosion treatment to enhance their visual effects and durability. Each step requires the craftsman's superb skills and patience to ensure that the finished product meets the expected quality standards.
6. Quality control and testing
After the casting is completed, the quality inspection of the product is crucial. Through microscopic analysis, ultrasonic testing or X-rays, it is possible to detect whether there are bubbles, cracks or other defects inside the casting. Only through strict testing can each casting meet the technical requirements and quality standards before it can be delivered to customers or put on the market.
7. Environmental and safety factors
The waste gas, dust and waste generated during the bronze casting process have a certain impact on the environment. Factories need to follow environmental regulations and use environmental protection technologies to reduce emissions. At the same time, the casting process involves high temperatures and hazardous substances. Workers need to be equipped with appropriate safety equipment and strictly abide by safety operating procedures to ensure the safety of the process.
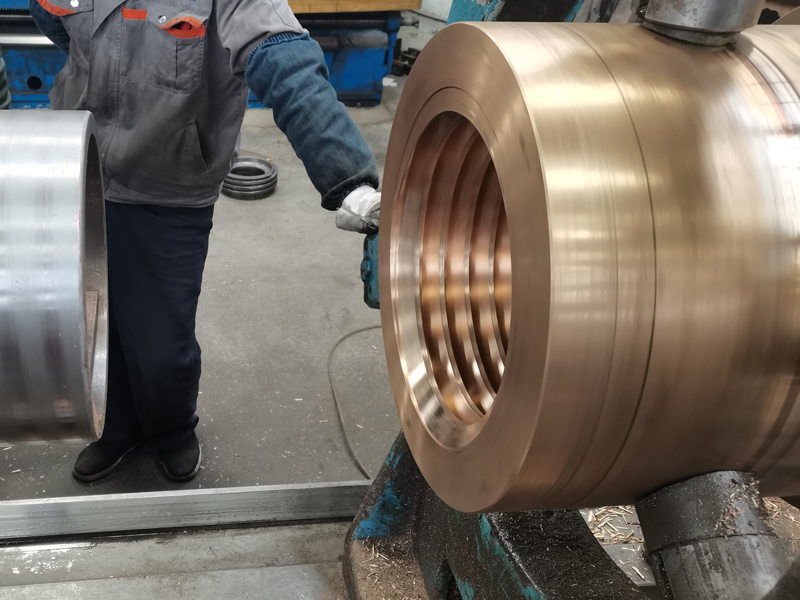
Summary
bronze casting is a complex process that combines art and technology. Details determine success or failure. Whether it is the selection of raw materials, the design of molds, or every link such as smelting, pouring, and cooling, they are all crucial to the quality of the final product. Only by paying attention to every detail and strictly controlling various parameters in the production process can high-quality bronze castings be created.
The essence of bronze casting is that it is not only a technical process, but also an artistic expression. By continuously improving the level of technology and striving for excellence, the bronze casting industry will continue to maintain its important position in the field of art and industry in the future.