Process analysis:
The flanging deformation of
brass bushings material is relatively complicated. During the expansion process, the material in the deformation zone is mainly subjected to tangential tensile stress, which causes tangential elongation deformation. After the expansion is completed, its stress state and deformation characteristics are similar to the inner hole flanging. The deformation zone is mainly tangential drawing deformation, and its limit deformation degree is mainly limited by edge cracking.
Considering that the production batch of parts is not large, and the above-mentioned processing procedures are more, which affects the improvement of economic benefits, and it is noted that there are 30mm×1.5mm brass tubes on the market, therefore, it is considered to use copper tubes to complete the processing of parts through direct flanging.
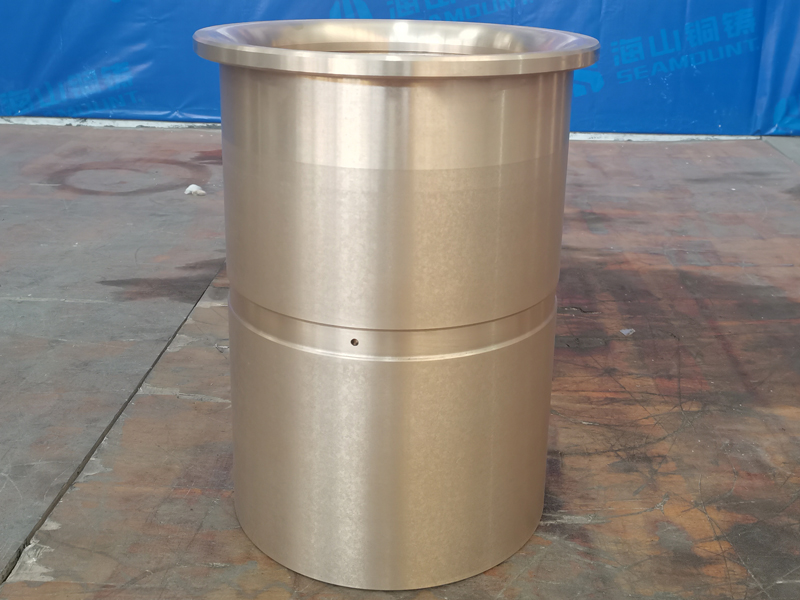
The shape of the part is simple, and the precision requirements of each dimension are not high, which is conducive to forming. According to the part structure, the most economical and intuitive process plan usually considers the use of flat blanks to directly form parts through inner hole flanging. To this end, it is necessary to first determine the maximum height of the part that can be achieved by flanging once.
Since the maximum flanging height of the part is much smaller than the height of the part 28mm, it is impossible to make qualified parts by direct flanging. To form the part, it must be deep drawn first. After calculating the diameter of the blank and judging the number of deep drawing of the flanged deep drawing part, it can be determined that the part adopts the deep drawing process. It must be drawn twice and then the bottom of the tube can be cut off before the processing is completed.
Hardness test:
Professional hardness tests all use Brinell hardness. Generally speaking, the smaller the Brinell hardness value, the softer the material and the larger the indentation diameter; conversely, the larger the Brinell hardness value, the harder the material and the smaller the indentation diameter. The advantages of Brinell hardness measurement are high measurement accuracy, large indentation area, and the ability to reflect the average hardness of the material in a large range. The measured hardness value is also more accurate and the data repeatability is strong. If you have any questions, please call us. Xinxiang Haishan Machinery is professional in solving various copper casting questions for you.