The dynamic pressure lubrication method of the ball mill main bearing bush refers to the use of an oil pump to send lubricating oil to the working surface between the bush and the main shaft through pressure, and lubrication is achieved through the action of the dynamic pressure oil film. This lubrication method is mainly used for high-speed equipment that carries a large load, such as ball mills.
Working principle of dynamic pressure lubrication:
Lubricating oil supply: The lubricating oil is sent to the lubricating oil inlet of the bearing through a special oil pump. The oil pump usually provides a certain oil pressure to ensure that the lubricating oil can effectively enter the gap between the bush and the main shaft.
Oil film generation: A lubricating oil film is formed between the main shaft and the bush. When the bearing is running, the surface of the bush and the surface of the main shaft move relative to each other, and the lubricating oil will form an oil film due to the fluid dynamics, thereby avoiding direct contact between the metal surfaces and reducing friction and wear.
Dynamic pressure action: The key to dynamic pressure lubrication is to generate pressure through the flow and relative movement of oil in the bush, so that the lubricating oil forms a stable oil film between the bush and the main shaft. The oil film can not only carry the bearing load, but also play a role in cooling, cleaning and corrosion prevention.
Lubrication effect: This lubrication method effectively reduces wear, lowers temperature, and improves the working efficiency and service life of the bearing. Under high load and high speed conditions, dynamic pressure lubrication can provide sufficient oil film thickness to prevent direct contact between the bearing and the main shaft, thereby reducing friction loss.
Advantages of dynamic pressure lubrication:
High load-bearing capacity: Dynamic pressure lubrication can provide a large load-bearing capacity and adapt to high-load conditions of large mechanical equipment such as ball mill main bearings.
Reduce wear: Effectively reduce direct contact between metals, reduce friction coefficient, and slow down the wear of bearings and main shafts.
Improve stability and efficiency: Through effective lubrication, the operating stability of bearings and the working efficiency of equipment can be improved, and the service life can be extended.
Cooling effect: Lubricating oil can take away the heat generated by the bearing, keep the working temperature within a suitable range, and prevent damage caused by overheating.
Application example: The bearing of the main bearing of the ball mill uses dynamic pressure lubrication, especially under high-speed rotation and heavy-load operation, which can effectively ensure the stability of the bearing system and extend its service life.
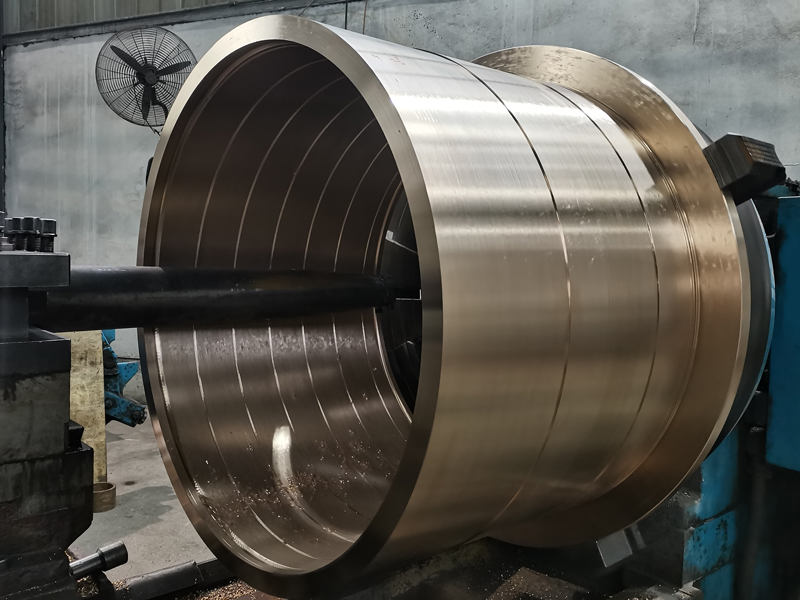
In general, dynamic pressure lubrication is an efficient and stable lubrication method, especially suitable for equipment such as ball mills with high loads and high speeds.