The performance test of the
copper sleeve of the crusher is crucial to ensure the stable operation of the equipment and extend its service life. Copper sleeves are usually used in the bearing parts of the crusher, and are subjected to high temperature, high pressure and wear. Therefore, the test of its performance needs to involve multiple aspects. The following are common methods for testing the performance of copper sleeves of crushers:
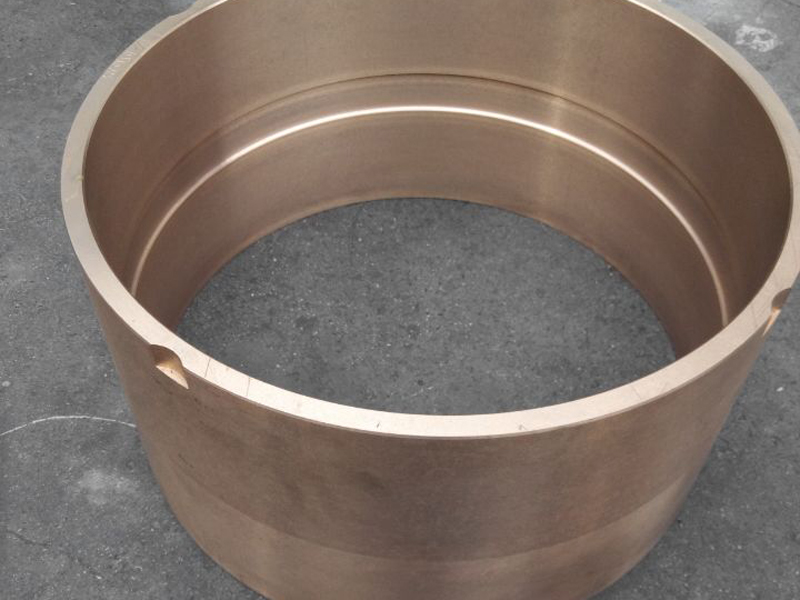
1. Hardness test
The hardness of the copper sleeve directly affects its wear resistance. Copper sleeves with insufficient hardness are prone to rapid wear. Common hardness test methods are:
Vickers hardness test (HV): suitable for small samples or thin parts, and can provide more accurate hardness values.
Rockwell hardness test (HR): used for hardness testing of metal materials, especially for larger samples.
Test purpose: to determine whether the hardness of the copper sleeve meets the design requirements, so as to ensure that it has sufficient wear resistance.
2. Wear resistance test
The wear resistance of the copper sleeve is the key to its long-term use in the high-load and high-wear environment of the crusher. Common wear resistance test methods are:
Friction and wear test: The friction coefficient and wear amount of the copper sleeve are measured by simulating actual working conditions through a friction tester.
Pin-on-disk test: The copper sleeve material is rubbed against a hard specimen to evaluate its wear performance.
Test purpose: To evaluate the service life of the copper sleeve in a high wear environment.
3. Compressive strength test
The copper sleeve needs to withstand the huge pressure transmitted by the crusher, so compressive strength is one of its key performance indicators. Common methods are:
Compression test: Apply different pressures on the test machine until the copper sleeve material is permanently deformed or ruptured.
Test purpose: Determine the bearing capacity of the copper sleeve under high pressure environment to prevent deformation or rupture during operation.
4. High temperature resistance test
The crusher generates a lot of heat during operation, and the copper sleeve may be exposed to high temperature environment, so its high temperature resistance is crucial. Test methods usually include:
Thermal expansion test: Measure the dimensional change of the copper sleeve at different temperatures.
High temperature tensile test: Test the tensile strength and elongation of the copper sleeve material at high temperature.
Test purpose: To evaluate whether the copper sleeve can maintain stable size and performance at high temperature.
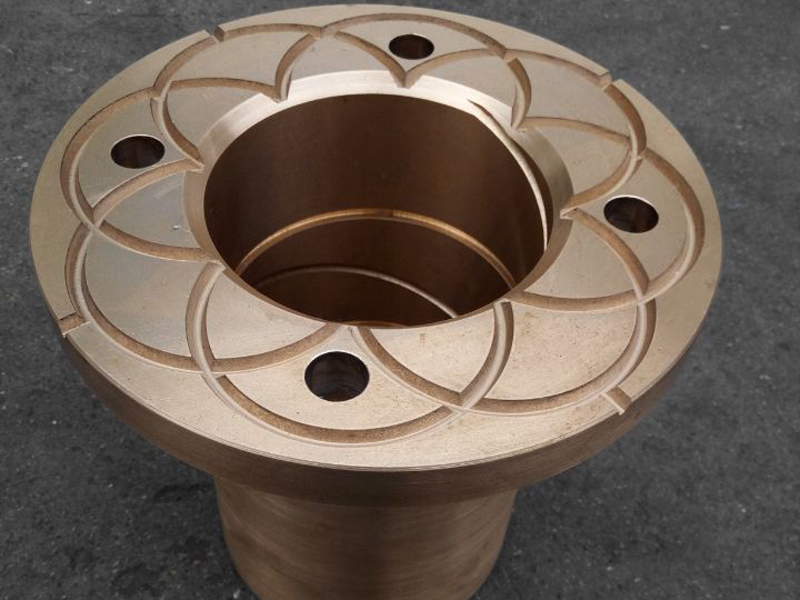
5. Chemical composition analysis
The material composition of the copper sleeve determines its performance, such as corrosion resistance and oxidation resistance. Common analysis methods include:
Spectral analysis: Use a spectrometer to detect the content of major elements in the copper sleeve, such as copper, tin, lead, zinc, etc.
X-ray fluorescence analysis (XRF): Non-destructive detection of the elemental composition of the copper sleeve material.
Test purpose: Ensure that the chemical composition of the copper sleeve meets the standard requirements to avoid performance degradation due to material problems.
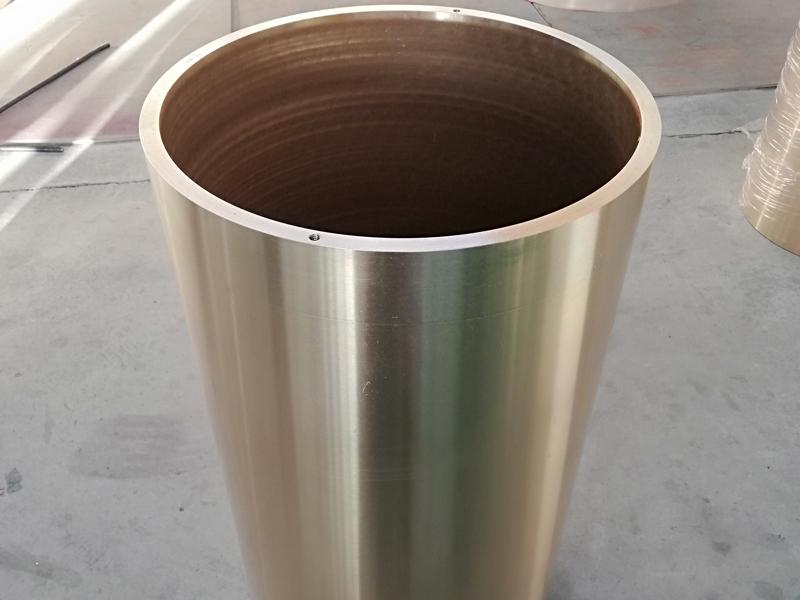
6. Dimension and tolerance inspection
The dimensional accuracy and tolerance of the copper sleeve are very important for its matching effect in the crusher. The test usually uses:
Three-coordinate measuring machine (CMM): used to measure the three-dimensional dimensions and geometry of the copper sleeve.
Vernier caliper/micrometer: used for simple dimensional measurement, check the diameter and thickness of the copper sleeve.
Test purpose: Ensure that the dimensions of the copper sleeve meet the design requirements to ensure its normal assembly and operation.
7. Corrosion resistance test
In harsh working environments, the copper sleeve may be corroded by moisture, chemicals, etc. Therefore, corrosion resistance is also a part of the test. Test methods include:
Salt spray test: Expose the copper sleeve to a salt spray environment to test its surface corrosion resistance.
Immersion test: Immerse the copper sleeve in different chemical reagents and observe its surface changes.
Test purpose: Ensure the durability of the copper sleeve in a humid or corrosive environment.
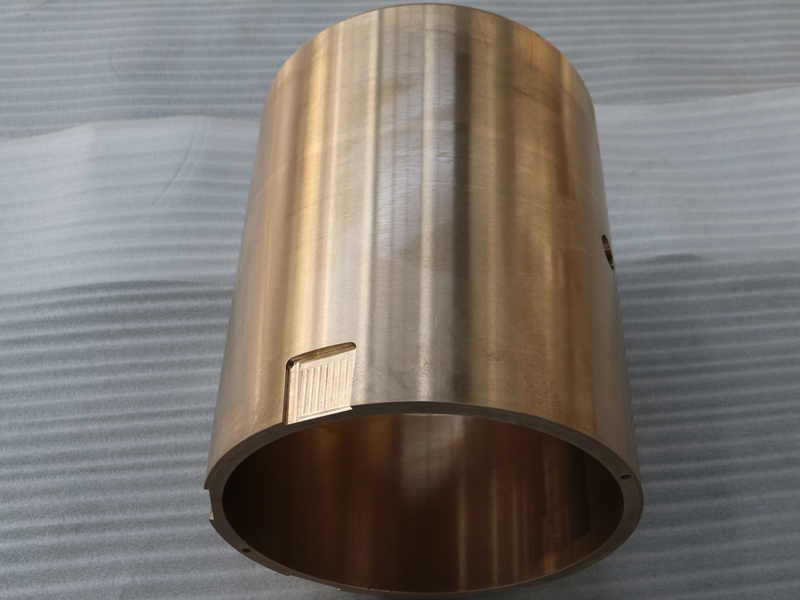
Summary
The performance test of the crusher copper sleeve covers hardness, wear resistance, compressive strength, high temperature resistance, chemical composition, dimensional tolerance and corrosion resistance. These tests can comprehensively evaluate the working performance and service life of the copper sleeve to ensure its stable operation in the crusher.