The mechanical properties of metal materials refer to the various mechanical properties of metals under the action of external forces. It is a measure of whether the metal can withstand working stress, deformation and damage under different loads, temperatures and environmental conditions. The mechanical properties of metal materials mainly include the following aspects:
1. Strength
Strength is the ability of metal to resist deformation or damage caused by external forces. According to the type of stress, strength is usually divided into the following types:
Yield strength: The minimum stress value at which metal begins to undergo plastic deformation when subjected to external forces.
Tensile strength (or tensile strength): The maximum stress that a metal can withstand during stretching.
Compressive strength: The maximum stress that a metal can withstand when under pressure.
Shear strength: The maximum stress at which shear failure occurs when a metal is subjected to shear force.
2. Hardness
Hardness is the ability of metal materials to resist local plastic deformation (such as indentations or scratches). Common hardness test methods include:
Brinell hardness (HB)
Rockwell hardness (HR)
Vickers hardness (HV)
Mohs hardness, etc.
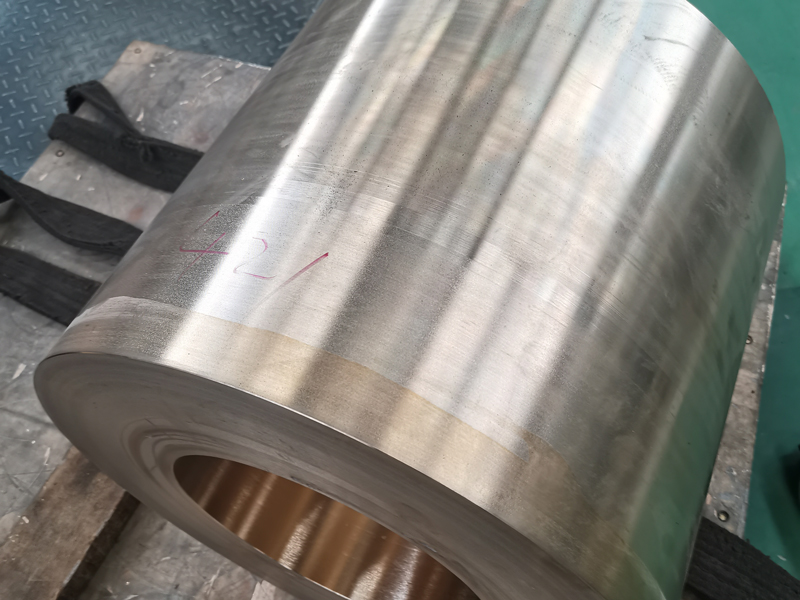
3. Plasticity
Plasticity is the ability of metal to undergo permanent deformation without breaking under the action of external forces. It is usually measured by the elongation or cross-sectional shrinkage of the metal. Metals with good plasticity can maintain structural integrity under large deformation and are not easy to break.
4. Toughness
Toughness refers to the ability of metal to absorb energy and undergo plastic deformation when subjected to impact loads. Materials with higher toughness can usually withstand sudden loads or impact forces and avoid brittle fracture. Toughness is often evaluated by impact tests (such as Charpy impact tests).
5. Fatigue strength
Fatigue strength is the maximum stress value that a metal can withstand under repeated or alternating loads. During long-term use, metal materials may produce fatigue cracks due to multiple loading and unloading, which eventually lead to fracture. Fatigue performance is usually tested through fatigue tests.
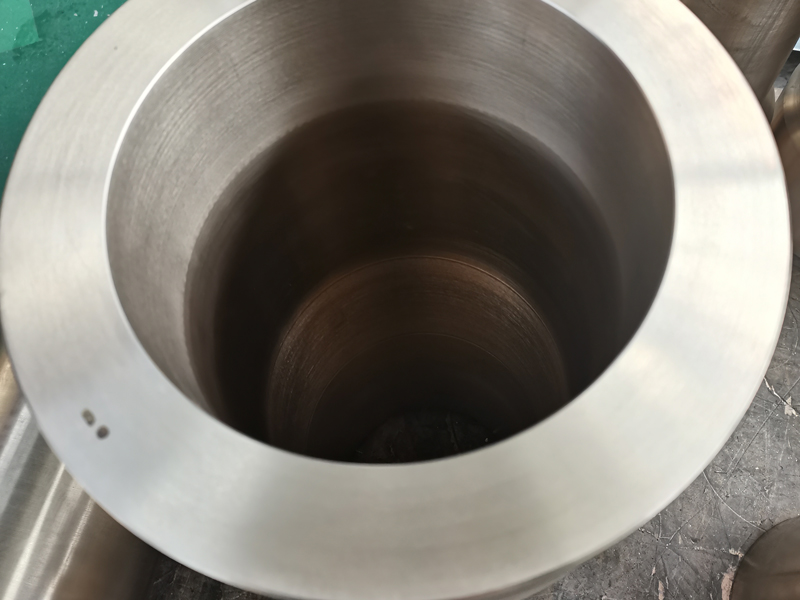
6. Creep resistance
Creep is the phenomenon that metals undergo slow plastic deformation under constant high temperature or high stress conditions for a long time. Creep resistance characterizes the ability of metals to work stably for a long time under high temperature and high stress environments. Creep properties are often evaluated through long-term creep tests.
7. Corrosion resistance
Although corrosion resistance is not usually a direct "mechanical property", it will affect the service life of the metal in the actual working environment. For example, some metals may become brittle in humid, acidic or other corrosive environments, affecting their mechanical properties.
8. Elastic modulus
Elastic modulus is the ability of a metal to resist deformation within the elastic deformation range, usually expressed by **Young's modulus (E)**. It represents the unit strain under unit stress. The larger the value, the harder the material and the smaller the deformation.
9. Fracture toughness
Fracture toughness is a measure of the ability of a metal material to resist crack propagation before crack propagation occurs. Higher fracture toughness means that the material is less likely to undergo brittle fracture when cracks exist.
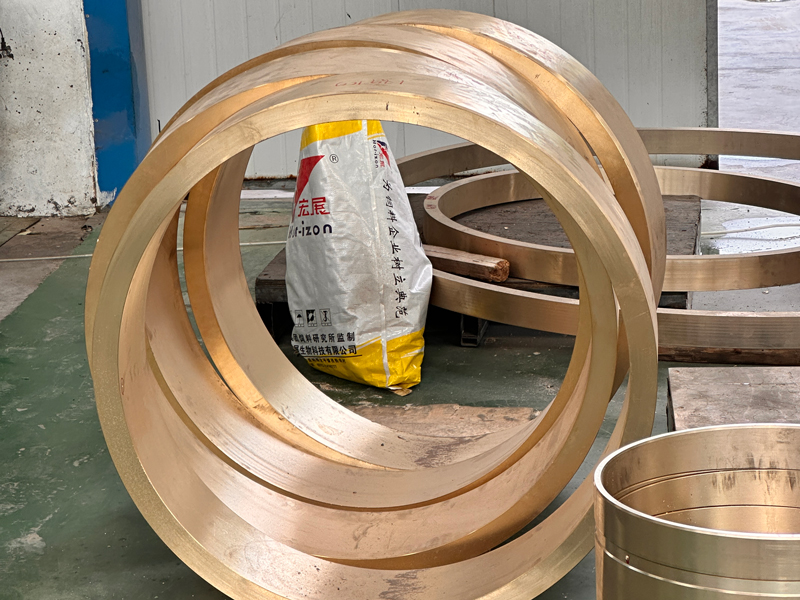
Summary
The mechanical properties of metal materials determine their performance in actual applications, such as load-bearing capacity, durability, operating temperature range, etc. Different metal materials have different mechanical properties and are suitable for different working conditions. In engineering design and material selection, it is necessary to comprehensively consider the various mechanical properties of metal materials based on actual usage conditions to ensure that they meet usage requirements and are reliable.