The centrifugal casting process and technical requirements of tin
bronze bushing mainly include the following aspects:
Casting process:
The centrifugal casting process of tin bronze bushing is a method of casting special castings such as rings, tubes, cylinders, bushing, etc. by using centrifugal force. During the casting process, the liquid alloy is filled and solidified under the action of centrifugal force to obtain a casting. The characteristics of this casting method are good metal shrinkage compensation effect, dense outer layer structure of the casting, few non-metallic inclusions, and good mechanical properties.
Technical requirements:
1. Melting link: The charge must be degreased and rusted, kept clean, and a covering agent such as charcoal should be added to the bottom of the electric furnace. The temperature of the copper liquid should be strictly controlled during smelting. It is usually necessary to pre-deoxidize the alloy at a high temperature of 1150~1200℃, and heat it to about 1250℃ for final deoxidation and refining.
2. Material control: When casting pure copper and tin bronze, attention should be paid to the restriction of impurity content, and avoid using iron tools, crucibles that have melted other copper alloys, and contaminated recycled materials. Tin bronze bushing have strong gas absorption. To reduce gas absorption, they should be quickly melted in a weak oxidizing or oxidizing atmosphere and under the protection of a covering agent.
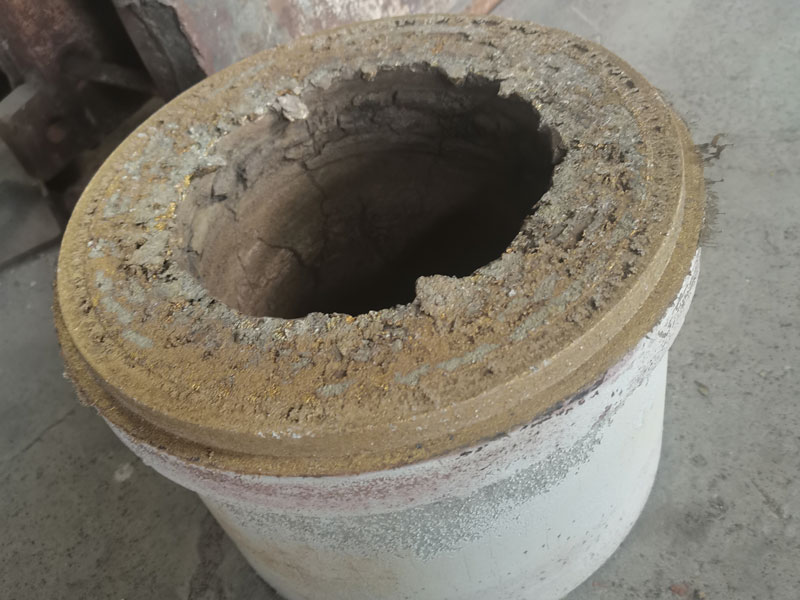
Please note that the above information is for reference only. The specific casting process and technical requirements may be adjusted according to the specific application scenario, material properties and customer needs. In actual operation, the relevant process regulations and safety operating procedures should be strictly followed to ensure the smooth progress of the production process and the stable quality of the product.