The difficulties in casting tin bronze bushings mainly include the following aspects:
1. Casting defects: Common defects in tin bronze casting include pores, pinholes, insect bites or local blackening on the casting surface, tin sweat or lead sweat, slag inclusions, segregation, shrinkage cavities, shrinkage, cold shut, etc. The causes of these defects may involve multiple factors such as severe alloy liquid air absorption, improper pouring temperature control, excessive moisture or impurity content in the molding sand, and unreasonable pouring system design.
2. Reverse segregation phenomenon: Tin bronze itself has the characteristics of reverse segregation, that is, the first condensed part contains a higher amount of low-melting-point tin, and the later condensed part contains a lower amount of tin. This phenomenon may cause the strength and water pressure resistance of the casting to decrease.
3. Shrinkage problem: Tin bronze has a wide crystallization temperature range, condenses in a sticky state, and is prone to shrinkage defects. Shrinkage will reduce the mechanical properties and density of the casting, affecting its service life and safety.
4. Casting process control: Casting
tin bronze copper bushings requires precise control of process parameters such as melting temperature, pouring speed, cooling speed, etc. to ensure the quality and stability of castings. In addition, the design and manufacturing accuracy of the mold also have an important impact on the performance of the final product.
5. Material selection: High-quality copper materials and alloy elements are the basis for ensuring product quality. During the casting process, it is necessary to select suitable alloy materials and proportions to meet the mechanical properties and corrosion resistance requirements of the castings.
Improvement measures
In view of the above difficulties, the following measures can be taken to improve the quality and performance of cast tin bronze copper bushings:
1. Optimize the casting process: Reduce the occurrence of casting defects by improving the pouring system, adjusting the melting temperature and pouring speed, and improving the properties of the molding sand.
2. Strengthen mold design and manufacturing: Improve the design measures and manufacturing accuracy of the mold to ensure the dimensional accuracy and surface quality of the casting.
3. Strictly control the material ratio and alloy element content: Select high-quality copper materials and alloy elements, and strictly control their ratio and content to ensure the mechanical properties and corrosion resistance of the castings.
4. Introduce advanced casting technology: such as centrifugal casting, vacuum suction casting and other advanced technical measures to reduce casting defects and improve the performance of castings.
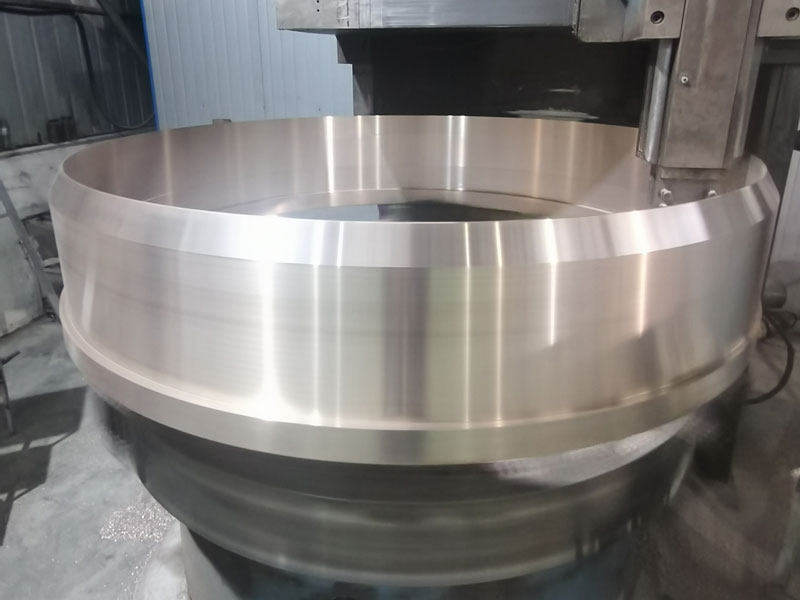
In short, casting tin bronze bushings requires comprehensive consideration of factors such as material selection, casting process, mold design and manufacturing to ensure the quality and performance of castings.