The first is the design craftsmanship of copper castings.
When designing, in addition to determining the geometry and size of the part based on the working conditions and metal material properties, the rationality of the design must also be considered from the perspective of casting alloy and casting process characteristics, that is, obvious size effects and solidification and shrinkage. , stress and other issues to avoid or reduce the occurrence of defects such as composition segregation, deformation, and cracking of copper castings.
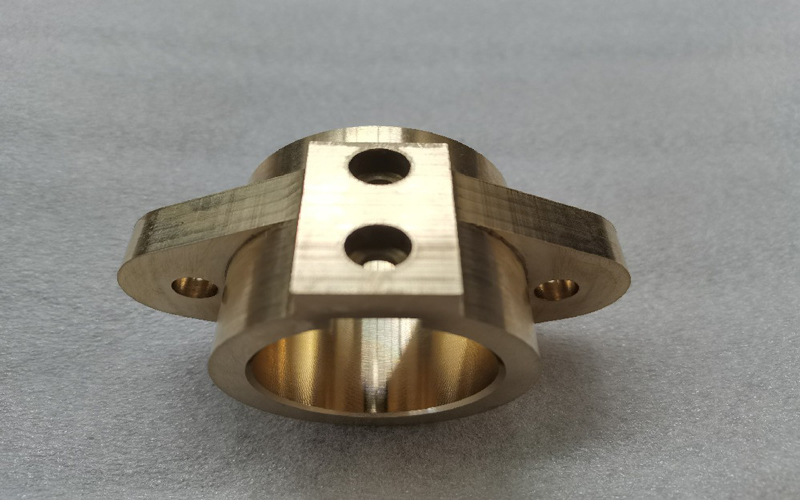
Copper castings
Second, there must be reasonable casting technology.
That is, according to the structure, weight and size of copper castings, casting alloy characteristics and production conditions, select the appropriate parting surface and shape, core making method, and reasonably set up casting bars, cold iron, risers and gating systems. To ensure high quality castings.
The third is the quality of raw materials used for casting.
The quality of metal charges, refractory materials, fuels, fluxes, modifiers, casting sand, molding sand binders, coatings and other materials is substandard, which can cause defects such as pores, pinholes, slag inclusions, and sand sticking in castings, affecting the appearance of copper castings. Quality and internal quality, in severe cases, the castings will be scrapped.
The fourth is process operation.
It is necessary to formulate reasonable process operating procedures, improve the technical level of workers, and ensure that the process procedures are correctly implemented.